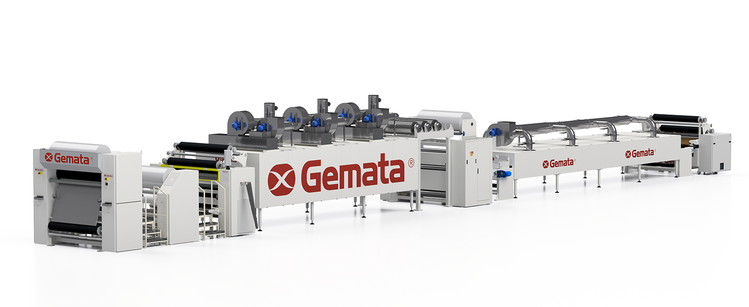
MULTI GREENFINISH is a multipurpose system designed for
the upgrading of ovine, half bovine, and calf leathers, intended
for leather goods and footwear applications by the use of:
- Release papers to create satin, nubuck, and fine grain surfaces such as nappa; by using release paper and appropriate chemical products, it is possible to achieve a fully finished leather, including the application of a fixative, in one single passage
- Embossing rollers for creating thicker grains, such as saffiano, reptile, and dollar patterns and more, protected by a thin film that shields the leather while simultaneously conveying it along the entire production line. Embossed rollers allow to customize the leather grain, which subsequently requires a topcoat application
These are two highly efficient ecological processes, the result of Gemata’s extensive experience in the finishing sector, which guarantee the production of excellent quality leather with reduced energy resources and zero emissions into the atomosphere.
MODEL | 1800 | 2200 | 2600 |
---|
WORKING WIDTH | 1700 | 2100 | 2500 |
---|
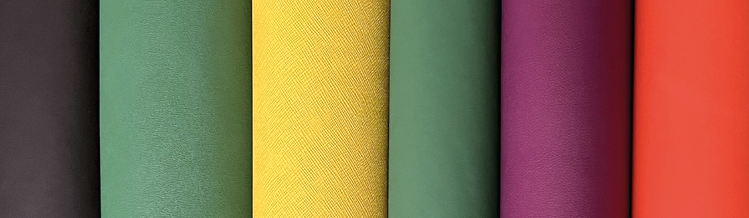
Leathers finished with release paper
Both configurations grant a uniform finish, free from surface defects, while maintaining the natural softness of the leather.
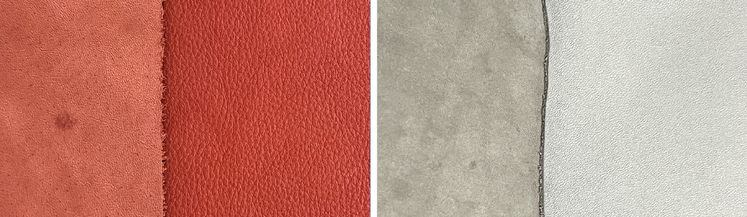
Leathers finished with protective film
TECHNICAL LAYOUT
- Finishing lines of compact overall dimensions
- Production speeds range from 6 to 12 m/min, depending on the length of the drying tunnels
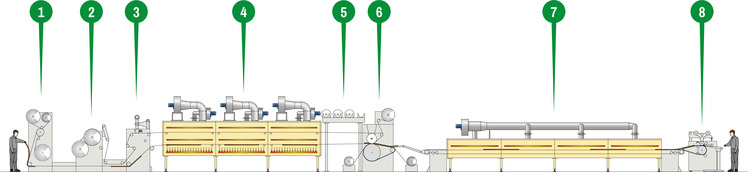
- DETACHING CONVEYOR TABLE; RELEASE PAPER CLEANING UNIT AND PAPER/PROTECTIVE FILM REWINDER; RELEASE PAPER OR PROTECTIVE FILM REWINDER
- TWO-STATION FIXED UNWINDER; JOINING TABLE UNIT
- GREENLINE 2R ROLLER COATING HEAD
- DOUBLE STARDRIER-IR INFRARED DRYING TUNNEL
- EMBOSSING CYLINDER STORAGE
- ROTARY MULTIPRESS
- STARDRIER-IR INFRARED DRYING TUNNEL
- GREENSTARs ROLLER COATING MACHINE
Throughout the entire process, the leather surface, being protected either by release paper or film, remains uncontaminated by dust. Leathers finished with the Multi Greenfinish system experience a reduced surface loss of 1.5% to 2.5% compared to traditional finishing methods, as leather remains “joined” to the surface of the paper or film during low-temperature drying.
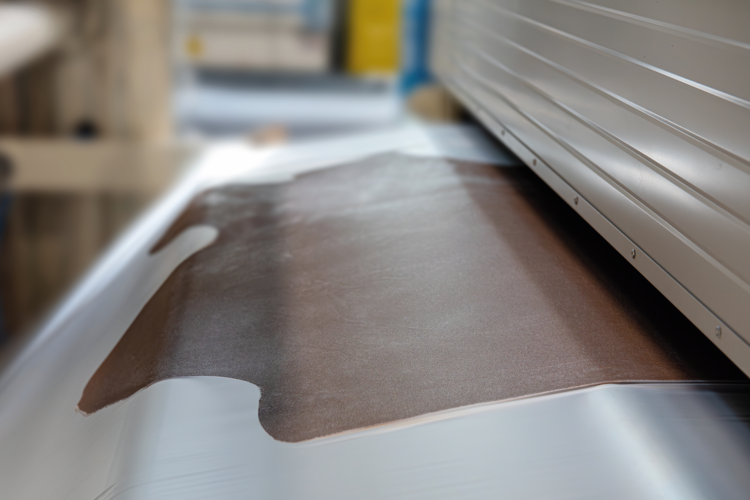
Leather joined to the surface of the protective film